Sustainable Smart Factory
A pilot project for an AI automated 3D printing facility, called Sustainable Smart Factory, was hosted in Plus X Innovation with a mission to develop a local, scalable manufacturing process that could transform how we design products, making them more efficient and less wasteful.
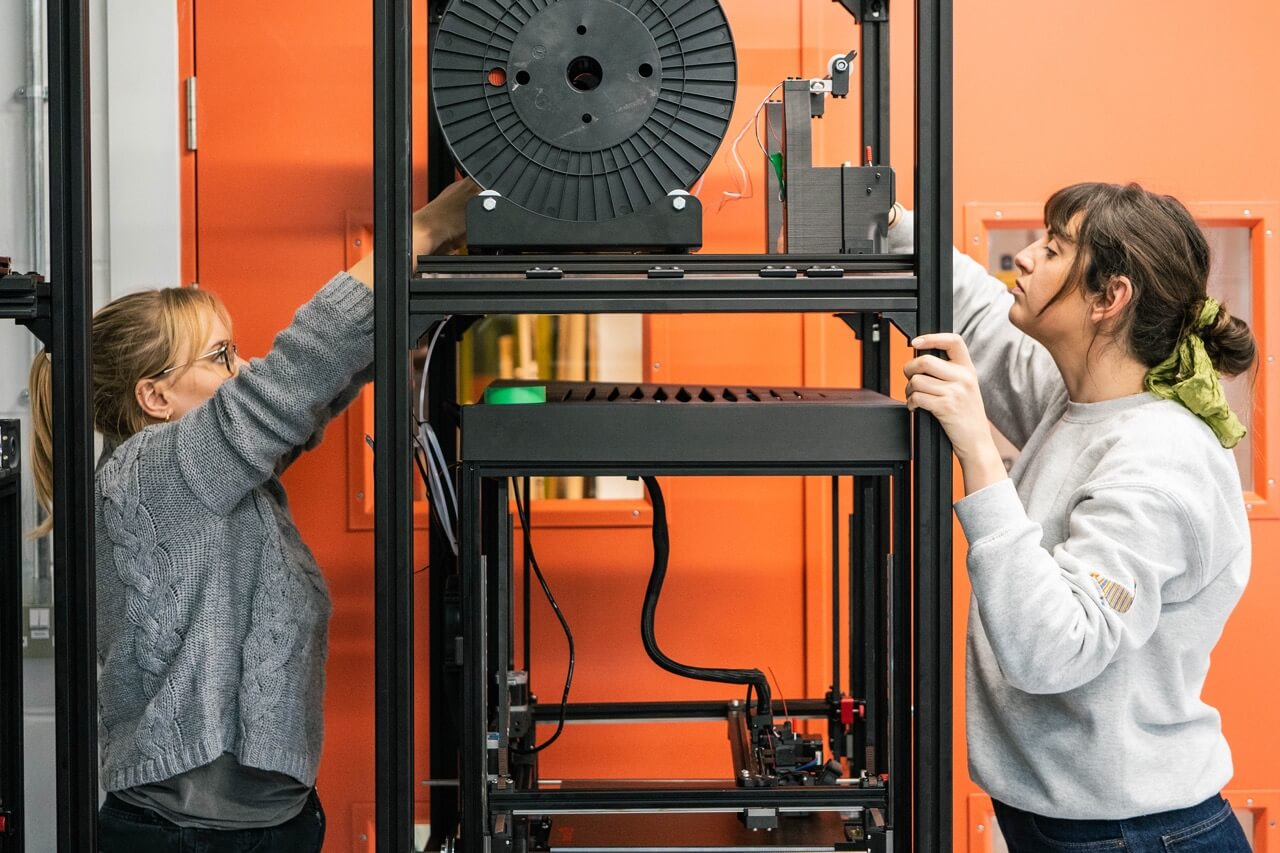
The Problem
3D printing has quickly become the dominant technology for small scale prototyping. But it is massively underutilised in manufacturing.
Why?
- There is a high fail rate, where the print fails during the production.
- There are high energy and resource waste levels, with the high fail rate.
- 3D printing also requires expert technicians to monitor the printing process, making it hard to scale.
- Design constraints which limit the mass manufacturing applications.
- 3D prints have a characteristic aesthetic which consumers don’t expect.
3D printing for manufacturing at scale, nevertheless, has huge potential: to enable more resilient supply chains, and bring products to market with greater agility.
As part of an £1.8m Innovate UK funded project, Plus X Innovation Brighton hosted the Sustainable Smart Factory (SSF) pilot demonstrator for an AI-optimised and automated 3D printing production line, trialling hardware from startup, Batch.Works and software from Cambridge University spinout, Matta Labs, utilising 160 sq ft of accessible technical workshop in Brighton.
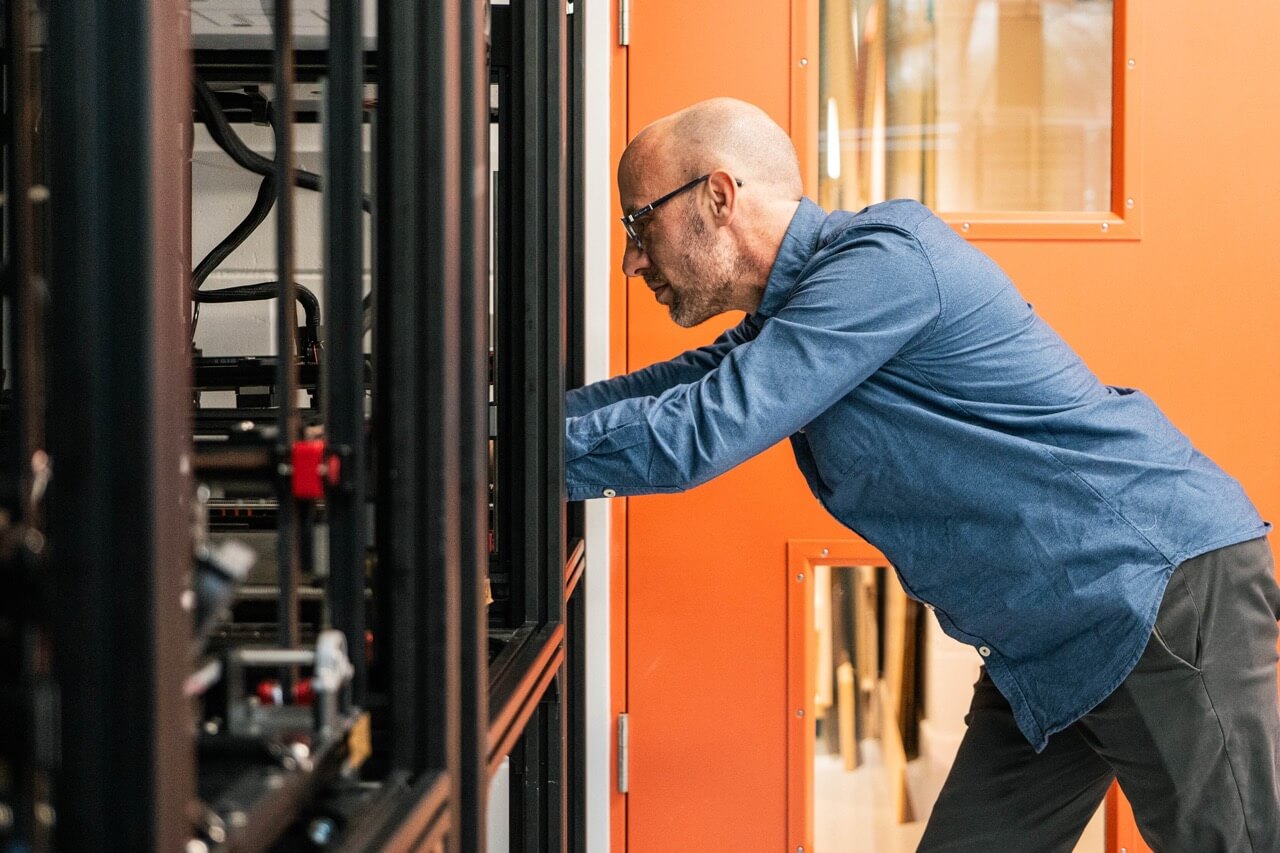
The Solution
The reputation of 3D printing as an exclusively prototyping technology is not accurate, and this partnership demonstrated the first test-pilot for remote automated manufacturing. The teams worked to deliver a scale-up plan for a distributed network of 3D printing factories across the UK.
Alongside hosting the demonstrator and developing a roadmap for future sites, Plus X Innovation developed and delivered a powerful programmatic intervention around sustainable manufacturing, to raise awareness and support with dissemination and engagement activities.
Some of the activities are highlighted below.
Student Design Brief, Plus X Innovation Brighton (with University of Brighton):
We hosted a session with the University of Brighton to demonstrate the latest advances in digital manufacturing to the next generation of Product Designers. This was to promote the opportunities that the technology presents to manufacture locally, with a circular flow of materials and take advantage of the possibilities for agile product development, extreme customisation and low-wastage production.
SME Design Brief, Plus X Innovation Central Research Laboratory:
SMEs worked with Batch.Works and Plus X Innovation on circular design and manufacturing techniques to explore how to make products free from the constraints of traditional mass manufacturing, including 1-to-1 sessions on design for manufacture (DFM) on the demonstrator.
Circularity Now event:
The right space is critical for the circular economy. We hosted an evening of talks and networking event to bring together people interested in circular design and manufacturing. As well as talks about the SSF project, we had panels and demos from other SMEs and organisations working in circular economy innovation, including Gomi, Marinatex, Disruptor.London, University of Sussex, Design Council. This event drew diverse attendees and encouraged collaboration and networking with over 100 attendees and was widely applauded by stakeholders.
.png)
The Outcome
The physical demonstrator of this 3D manufacturing at scale meant the teams gained insight about the implementation of integrating into a real-world scenario. It also resulted in valuable data about introducing the technology to potential users, with understanding of their needs and their use cases.
This project also achieved its goal to improve the accuracy of the AI model, through the direct printing of thousands of parts and learnings through trial and error. Ultimately this created a business case for a future distributed 3D printing manufacturing facility that could be part of a reshoring manufacturing strategy.
This demonstrator serves as evidence of what can be achieved through collaboration, innovation, and a strong commitment to sustainability.
Impact Stats:
- 160 sq ft of accessible technical workshop in Brighton used for Demonstrator
- 2,153 parts printed using AI optimised 3D printing production facility
- 100+ attendees and notable circular manufacturing industry and academic leaders attended Circularity Now event
- 21 students and 14 SMEs supported to imagine new ways of designing products for the new generation of on-demand digital manufacturing technology
.png)
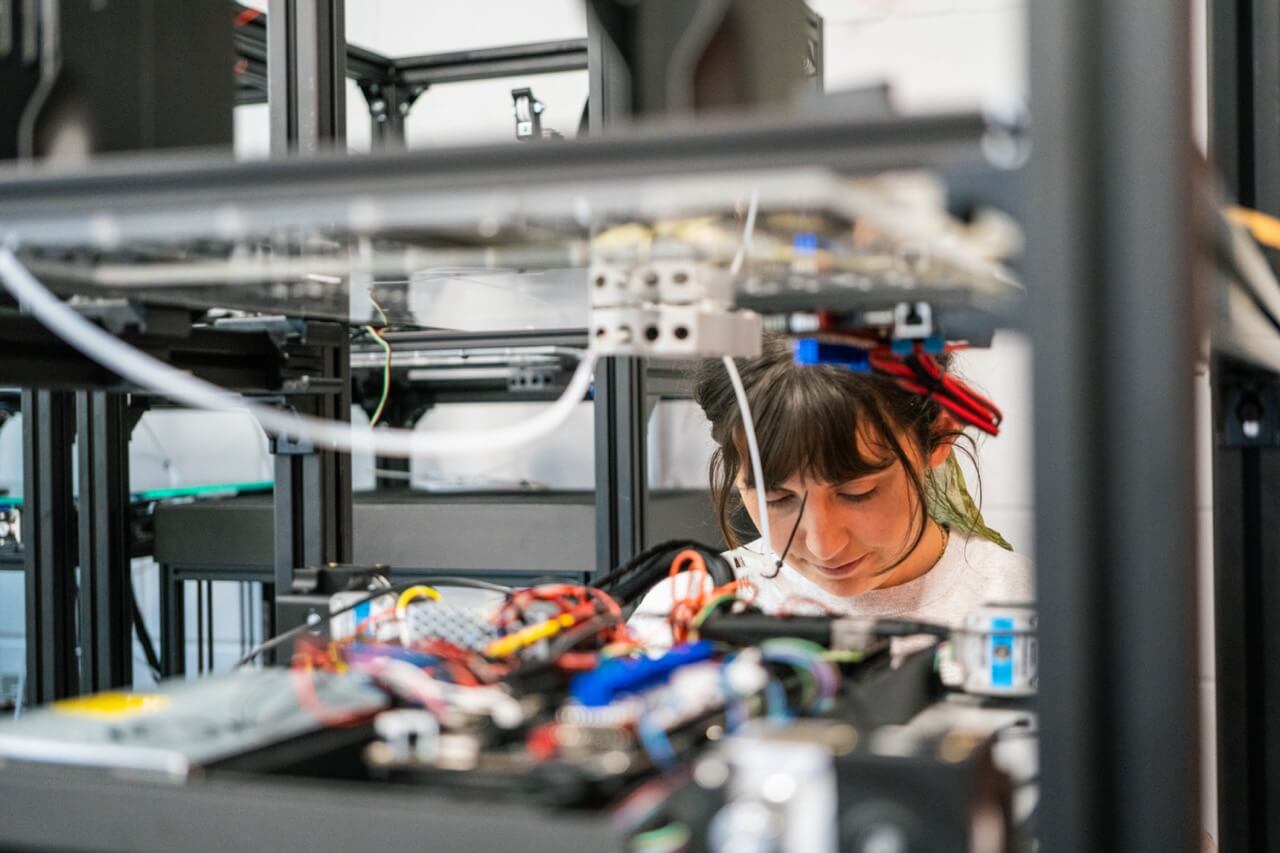
Continue reading
Book a consultation
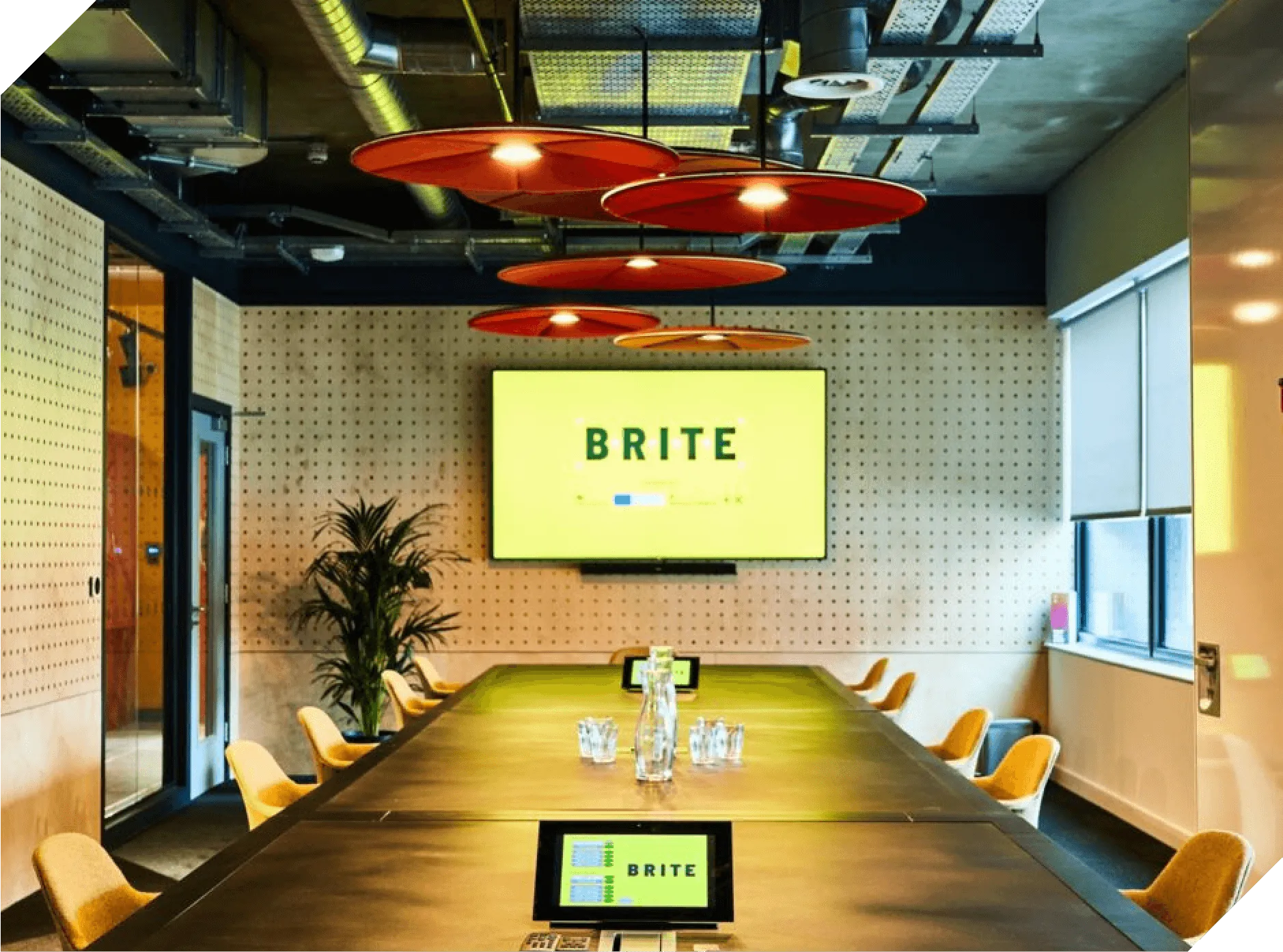